EV Battery Testing Methods
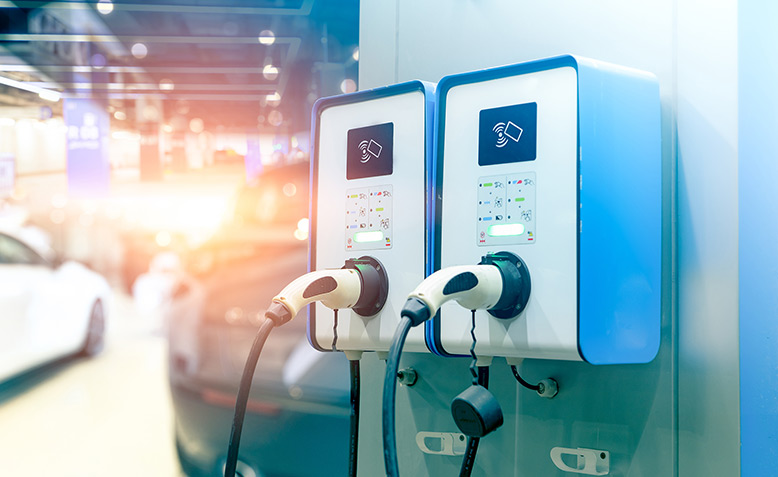
What is EV Battery Testing Equipment?
EV battery testing equipment measures, charts, and manages the life cycle of battery systems within electric vehicles (EVs).
As the world progresses toward electric-powered vehicles, having powerful and functional batteries is more important than ever. Battery systems are vital to many operations within a vehicle, from turning the lights on to powering the engine.
Regular tests during a battery’s development are necessary to prevent outages, as capacity drops long before life expectancy and weak cells can cause expensive failures. In the case of electric vehicle (EV) battery testing, the equipment diagnoses battery health by way of voltage, impedance, and storage capacity. The diagnostic is a concise report of how long the battery will be able to supply power to the vehicle and whether it will be able to operate at maximum functionality.
There are many functionalities within the umbrella of EV battery testing. To determine what kind of equipment is ideal for your application, it’s helpful to know the different types of battery testing.
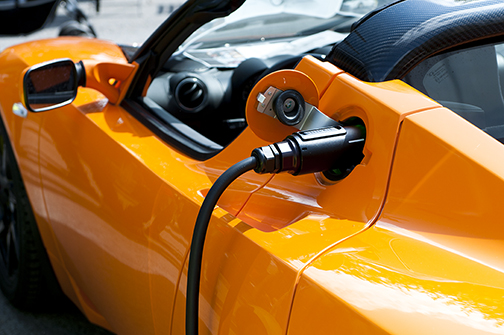
Though the focus of this page is electric vehicles, battery testers are required for a diverse array of tests from life cycle testing to cell balance verification. The following are common uses: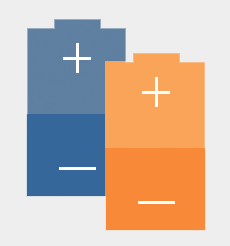
Choosing the right testing equipment for your application can be a difficult process. Test systems are costly, replacing them is time-consuming, and installing them brings both active and backup systems to a halt. Renting a battery tester is often the best option: you get the industry’s best equipment for a fraction of the price and a rental period that is flexible to your test schedule. Consider the following when selecting your battery tester machine:
Any other questions? Reach out to one of ATEC’s battery test specialists for assistance.
Regular tests during a battery’s development are necessary to prevent outages, as capacity drops long before life expectancy and weak cells can cause expensive failures. In the case of electric vehicle (EV) battery testing, the equipment diagnoses battery health by way of voltage, impedance, and storage capacity. The diagnostic is a concise report of how long the battery will be able to supply power to the vehicle and whether it will be able to operate at maximum functionality.
There are many functionalities within the umbrella of EV battery testing. To determine what kind of equipment is ideal for your application, it’s helpful to know the different types of battery testing.
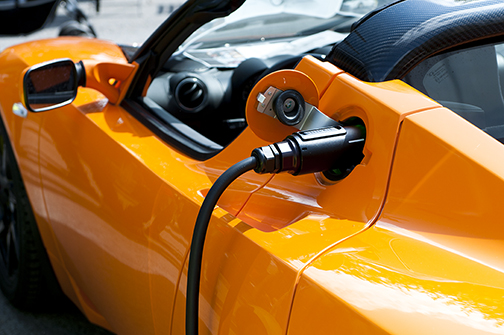
What are Some Methods of EV Battery Testing?
EV battery testing consists of several methods performed both on each battery cell within the EV and the entire battery system. These tests take the battery through every type of use and possible abuse to ensure compliance and safety.- Impedance tests are performed on a power line to discover weak battery cells prior to failure.
- Battery discharge testing, also known as capacity or load testing, is performed off the line and tests the performance of the entire battery system, demonstrating how it will interact with a load in real-world conditions. This test is often performed with a chiller that dispels the battery’s heat as it discharges.
- Cycling, also called aging, is an accelerated life cycle test to assess whether the battery can meet its life cycle requirements.
- Cell level and level pack testing test the individual components (down to a cell level) compared to the entire system.
- Temperature performance assesses how the battery will perform in different temperatures.
- Overcharge and overdischarge tests assess how the battery reacts to either too much or too little voltage to measure its safety.
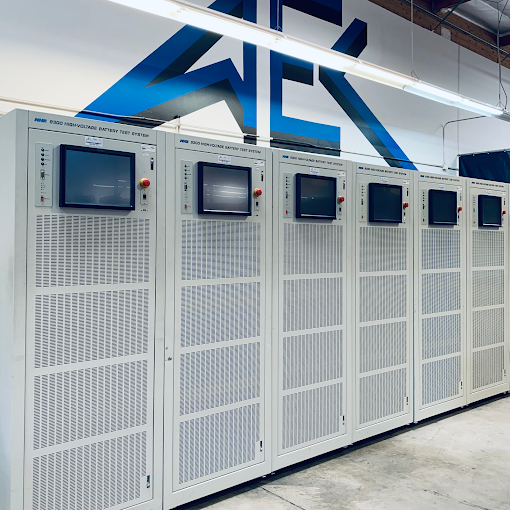
EV Battery Testing Standards
Some common test standards to follow when looking at EVs specifically are:
- UL 2580
- IEC 62133
- IEC 62660
- ISO 12405
Battery Test Equipment Applications
Leading test systems are programmable and regenerative. Programmable systems allow for complete flexibility and control of the test, with each channel tested independently. Meanwhile, regenerative systems return discharged power back into themselves, greatly reducing power consumption.Though the focus of this page is electric vehicles, battery testers are required for a diverse array of tests from life cycle testing to cell balance verification. The following are common uses:
- Life cycle testing
- Electric vehicle (EV) testing
- Electrochemistry testing
- Supercapacitor testing
- Electrochemical impedance spectroscopy (EIS)
- Coulombic efficiency testing
- Simulating real-world test scenarios
- Research & development for products, vehicles, and grid storage
- Validating battery management systems (BMS)
- Testing smart battery modules
- Hybrid pulse power characterization testing (HPPC)
- Dynamic stress testing (DST)
- Testing lithium, nickel, lead/acid, sulfur, silicon, and more types of batteries
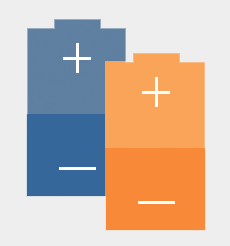
Choosing the right testing equipment for your application can be a difficult process. Test systems are costly, replacing them is time-consuming, and installing them brings both active and backup systems to a halt. Renting a battery tester is often the best option: you get the industry’s best equipment for a fraction of the price and a rental period that is flexible to your test schedule. Consider the following when selecting your battery tester machine:
Choosing the Right Battery Testing Equipment
-
Battery Type
- Look for a battery test system offering high-precision, integrated energy storage testing for both lithium-ion batteries and others.
-
Basic Functions
- A battery tester machine should be able to diagnose charge and discharge rate, state of charge (SOC) and state of health (SOH), depth of discharge (DoD), and take highly accurate voltage, current, temperature, and power measurements, both statically and dynamically.
-
Regenerative Capabilities
- Regenerative systems recycle energy from the battery to the electrical system or connected grid.
-
Upgrades
- Most modern equipment is customizable, offering upgradeable multi-channel test capabilities.