Multipaction Testing
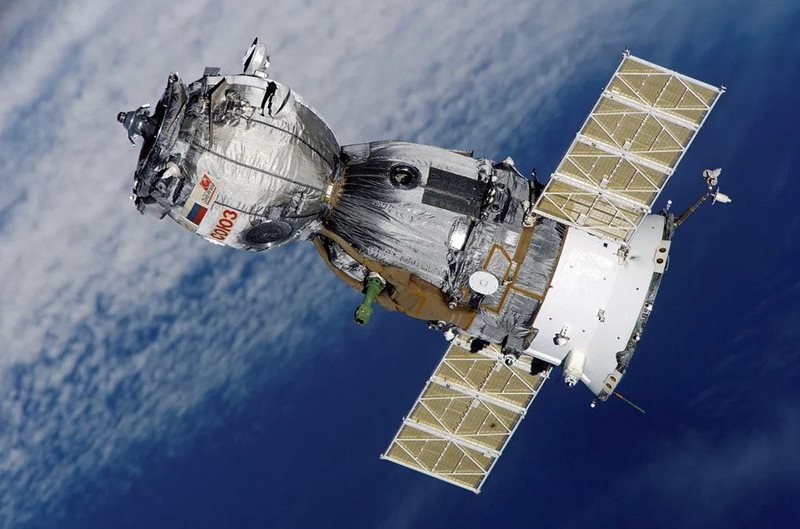
Multipaction—a portmanteau of "multiple” and “impaction”—is a term that describes an electron avalanche triggered by RF in a vacuum environment. Multipaction is the result of RF signals accelerating free electrons towards the walls of a component, in most cases a waveguide, with enough energy that their impact creates secondary electrons. The electrons multiply rapidly, building and building into what is called an electron avalanche, which in turn causes electrical discharges. Multipaction only occurs in vacuum environments like space because electrons collide with air in most environments, slowing them down and decreasing their potential to release secondary electrons. Satellite components are the most common victims of this phenomenon due to their repeated exposure to high power RF emissions in space.
There are two types of multipaction: single-surface and two-surface.
Single-Surface (Dielectrics)
For multipaction to occur, there must be an RF source, free electrons and a vacuum, and the following conditions must be met:
Testing reveals the device’s multipactor threshold, the level of RF power that the device can withstand without damaging itself. The multipactor threshold of a device should exceed the operating power by at least 6 dB.
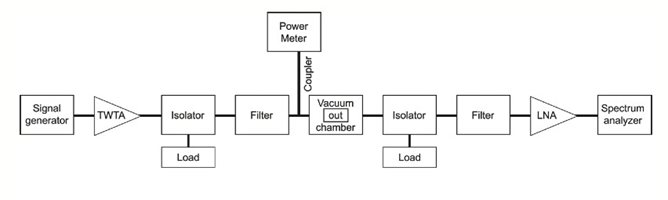
*Figure 1-2 was data retrieved from Rodriguez, Troy, et al. DESIGN, MANUFACTURE AND TEST TECHNIQUES FOR MULTIPACTOR FREE RF DEVICES. Sierra Microwave Technology, 9 Dec. 2019.
There are two types of multipaction: single-surface and two-surface.
Single-Surface (Dielectrics)
- Occurs on the dielectric surface of a component.
- The arcing of electrons across a narrow gap between two metallic surfaces.
For multipaction to occur, there must be an RF source, free electrons and a vacuum, and the following conditions must be met:
- Free electrons are available to start the release of secondary electrons, and the average number of electrons released is greater than one.
- The mean free path of electrons is much greater than the spacing between opposing surfaces.
- The time for an electron to travel from surface to surface is equal to an integer multiple of one-half of the RF period.
Measuring the Multipaction Threshold
Multipaction testing is divided into two types: global and local testing. Global tests assess the potential for the multipaction in a whole system, offering a positive or negative response as to whether it is present. In a global test, the tester recreates the operating conditions of an entire antenna system and monitors for the following performance changes for indications of multipactor effects:- RF noise levels close to the carrier
- 2nd and 3rd harmonic levels
- Output power variations
Testing reveals the device’s multipactor threshold, the level of RF power that the device can withstand without damaging itself. The multipactor threshold of a device should exceed the operating power by at least 6 dB.
Test Setup
The following diagram demonstrates a basic test setup for multipaction testing.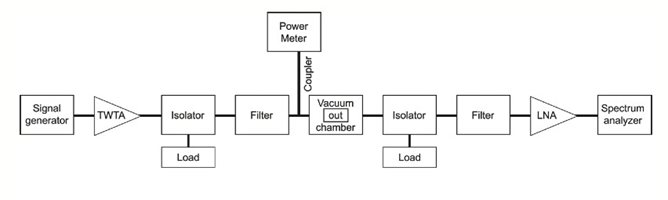
Test Equipment
To test for multipaction, test engineers require the following: 1) a means to produce modulated test signals; 2) an amplification device; and 3) the capacity to couple a part of the output signal from the DUT to a signal analyzer. The following are devices that fulfill these needs:- Amplifiers:
- TWT AMETEK/IFI PT86-6KW-TMS (Peak Amp)
- TWT AMETEK/IFI T8479-800-1200P (CW Amp)
- RF Signal Generator:
- Spectrum Analyzers | Signal Analyzers:
- Attenuator:
- Keysight 8491A 10dB Attenuator or equivalent
- Keysight 8491A 6dB Attenuator or equivalent
- Fairview Microwave SA 18N-30 30dB Attenuator or equivalent
- RF Power Meters | RF Power Sensors:
- Data Loggers:
- Vacuum Chamber:
- LACO VC-2000 Thermal Vacuum Chamber
- Function Generators:
- RF Passive Components:
- Couplers:
- DDCC-WR112-50F-30R Crossguide Coupler
Test Procedure
Certain test conditions must be met if multipaction testing is to be performed.How to Check Conditions for Multipaction Testing
- Test set-up calibrated prior to testing
- Multipaction standard used to verify the test set-up
- Power level ramped from 1600 Watts peak, 315 Watts average to 3000 Watts peak, 600 Watts average, in 200 Watts intervals with 5 minutes dwell at each level. 30 minutes dwell at maximum power of 3000 Watts peak, 600 Watts average
- Forward, reflected and output powers continuously monitored and recorded
- Third harmonic signals at input and output continuously monitored and recorded
- Current probes (Pico ammeters) placed at all ports through the vent holes to detect possible anomalies
- Several thermocouples placed on DUT and base plate to continuously monitor and record the temperature
- Thermal vacuum chamber pressure continuously monitored
- Visual inspection after multipaction testing using a microscope
Test Parameters
Figure 1 below demonstrates multipaction test parameters. This includes the RF signal waveform, the detection methods and number of units tested.Parameter | Setting | Notes |
---|---|---|
Frequency | 7.0 GHz | |
Power | 3000 W peak | 600 W average |
Pulse Width | 100 µs, 5% duty factor | |
Pressure | <1.0e-5 Torr | |
Temperature | -10 and +23 Deg. C | |
Electron Source | Cs—137 source | 3 sources, 10 µc each |
Sample Rate | 50 kHz | |
Detection Methods | Input return loss, through power | Instant change in any two parameters and/or anomaly in Pico ammeters, as recorded on a chart recorder/data logger. |
Input/Output third harmonic | ||
Current Probes (all ports) | ||
# of Samples Tested | 20 |
*Figure 1: Multipaction test parameters
Figure 2 demonstrates the Multipaction Test setup with EUT inside a thermal vacuum chamber. In this picture, the positions of thermocouples, current probes, and electron sources can be seen.
*Figure 2: Images of the circulator in the thermal vacuum chamber, including temperature sensors, current probes and Caesium electron sources
Software Tools
Multipaction software tools are used in tandem with EMC test equipment to create 3D simulations, determine breakdown levels, help in RF passive component design, and more. The following are commonly used variants:Software | Free? | Developer | Functionality |
---|---|---|---|
ECSS Multipactor Tool | Yes | Euorpean Space Agency | Takes ESTEC multipactor pre-calculated susceptibility charts for Alodine, Sliver, Gold, Copper and Aluminum, and determines breakdown levels. Not a multipactor simulation tool. |
CST Studio Suite | No | Dassault Systemes | RF field simulation software for 3D EM analysis. Results from simluations can be imported into Spark 3D for vacuum breakdown/gas discharge analysis. |
Spark3D | No | Dassault Systemes | Multipactor effect simulation tool for determining RF breakdown power level in passive devices like waveguides. CST Studio Suite simulations can be imported into Spark3D for vacuum breakdown/gas discharge analysis. |
Fest3D | No | Dassault Systemes | Analyzes complex passive microwave components; offers all capabilities necessary for passive component design. |