Aircraft EMC Testing
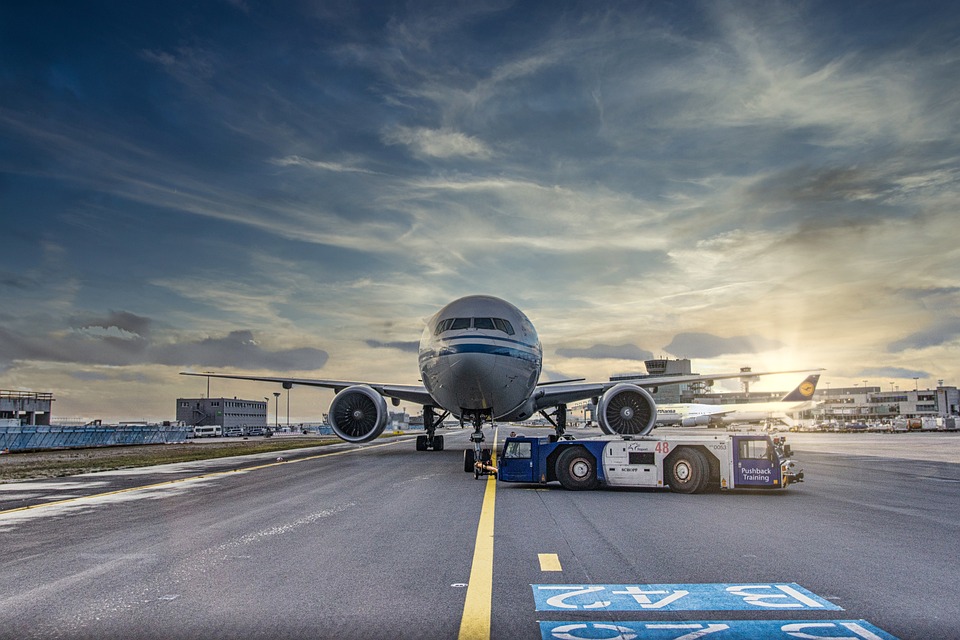
What is Aircraft EMC Testing?
Aircraft EMC testing determines aircraft compatibility with its electromagnetic environment to identify potential interferences. Sources that can produce EMI, such as natural impacts like environmental or thermal stimulants. For example, solar flares and radiation can produce unexpected surges that damage electronics, in this case – aircraft. Other electromagnetic interferences are signals created by machinery, cellular networks, and more. Electromagnetic pulses and transients occur in short surges of energy that can be either an isolated event or a series of bursts. Continuous EMI and isolated interferences can affect aircraft functions.
Aircraft EMC Testing Process
EMC testing for aerospace applications happens in various stages of airplane manufacturing. Conducting pre-compliance testing is often performed to save time in the long run. Larger electronic components are often tested in an open area test site (OATS). An alternative testing location is in a reverberation chamber like a semi-anechoic chamber.
Benefits of Aerospace EMC Testing
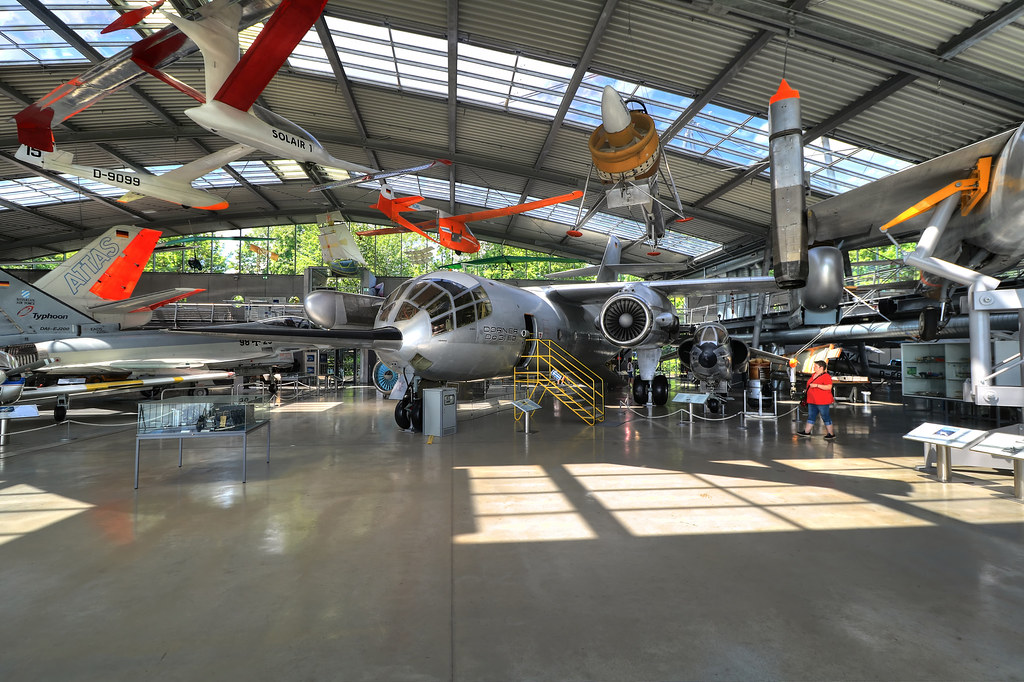
Expertise in aircraft design and engineering can minimize risks, but it is still easy to encounter hazards such as electrical issues that can cause malfunction or other problems on the aircraft. To maintain communication, navigation, and safety, it is essential to conduct electrical-related testing like EMC testing throughout the review and solution. EMC/EMI aerospace testing analyzes potential electrical threats that can occur to devices and equipment. For example, if currents pass through an electronic system with electromagnetic radiation, the testing can identify these problems.
There are various devices and equipment in aircraft that generate frequencies, such as radio networks and radars. To operate airplanes safely, there is an assortment of data-collecting instruments (receivers, analog, wireless synthesizers) to determine environmental conditions and analyze changes in the surroundings.
Avionic control systems reinforce throughout aircraft ascending, rolling, rotating, and landing. These movements rely on careful aerodynamics considerations, while the control systems receive commands from electronic interface and computing that opens the possibility of electromagnetic interference.
Types of Aircraft EMI/EMC Testing
EMC testing is particularly significant in the aerospace industry due to the aircraft’s proximity to storms and other dangerous environmental elements. The different types of aircraft EMC/EMI testing include testing on commercial aircraft, military aircraft, and single-source elements.
Aircraft EMC Testing Equipment
Comprehensive EMC testing comes across various equipment. The list below is the common aerospace testing equipment:
- Attenuators and resistors
- Current probes
- Capacitors
- Directional couplers
- Data recording devices
- Dummy loads
- Line impedance stabilization network (LISN)
- Isolation transformers
- Oscilloscopes
- Measurement receivers
- Power amplifiers
- Signal generators
- Rejection networks
Commercial Aircraft EMI/EMC testing
Commercial aircraft include airplanes that transport passengers, mail, can cargo, both domestically and internationally. Most civilian aircraft adhere to FCC standards (Federal Communication Commission) for radio transmission and EMI-permeable devices regulation.
Military Aircraft EMI/EMC testing
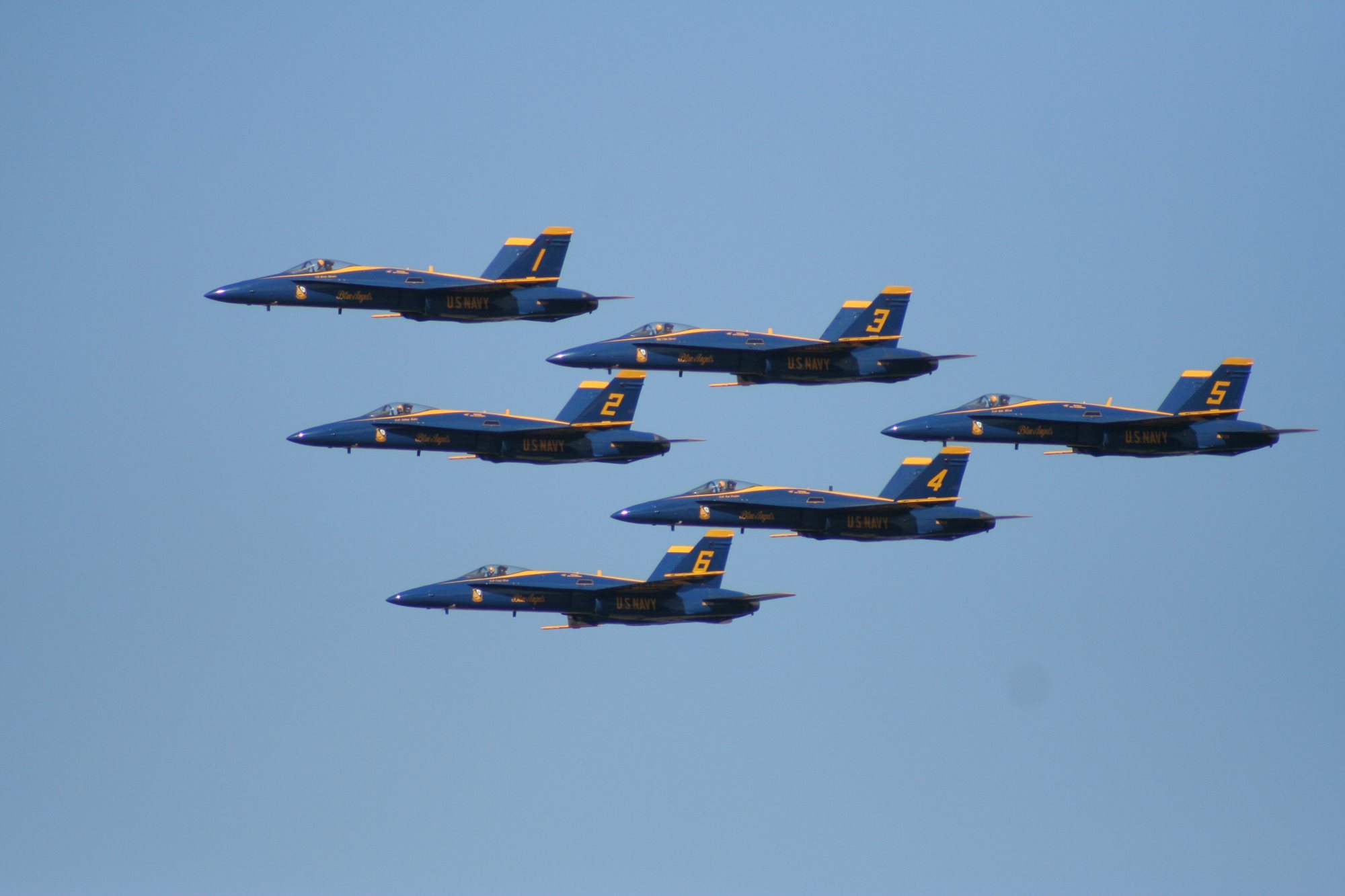
Military aircraft EMC testing follows the standards established by the Department of Defense (DoD), specifically MIL-STD-461 which includes guidelines for missions and susceptibility testing. There is also a supplemental standard to clarify testing methods for reviewing EMI.
- MIL-STD 461
- MIL-STD 462
- MIL-STD-1399
- DEF STAN 61-5
- DEF-STAN 59-411
Single-source Aerospace EMI/EMC testing
- Battery Testing
- Chemical Exposure Testing
- Dynamics Testing
- Environmental Simulation
- Fuel System Testing
- Hydraulics Testing
- Radio Testing
- Product Safety